How to Build a Safe EV Pack (Even Though Cells Sometimes Burn Up)
In recent times, the news has been replete with the kind of stories that strike fear into the hearts of battery engineers: Fires. Recalls. More fires. More recalls.
In October of 2020, Ford recalled approximately 20,500 Kuga plug-in hybrid crossovers and halted sales, due to concerns that the battery packs could overheat and catch fire. The recall cost $400 million. In February of this year, Hyundai’s Kona crossover was recalled due to fire hazards. Eventually, the recall will cost around $900 million. In August, GM announced they’ll spend close to $2 billion to recall Chevy Bolt EVs due to battery fires.
We could go on. These stories stress that – even though the electrification of the world is exciting; even though batteries are playing a greater and greater role in every industry – there are big challenges ahead. And one of the biggest is safety. Batteries are dangerous if not used correctly.
What can engineers do? Root-cause analysis by automotive OEMs has pointed the finger at cell-level defects. Cell quality is important, but the bigger reality is this: there is no such thing as a perfect battery. We will never rid battery packs of bad cells.
The good news is that it is still possible to build a safe EV battery pack. It just requires working from the start with this reality in mind.
The Dangers Caused by Cell-Level Defects
Almost two decades ago, the news began to fill with stories of lithium-ion batteries spontaneously combusting. These batteries resided inside laptops and other electronic devices. This worrying issue – caused by thermal runaway – has led to recalls by companies like Dell, HP, Lenovo, and even Apple. This past August, an airline passenger’s Samsung Galaxy A21 caught fire, causing major disruptions and major headlines. In January of 2019, the US Product and Safety Commission recalled approximately 78,500 HP laptops due to “fire and burn hazards.”
These fires have been a factor ever since the lithium-ion battery was first introduced. Way back at the dawn of the modern EV industry, Tesla began trying to build the biggest lithium battery packs to date. They wanted to see what would happen if one cell in a big pack were to burn. During nighttime experiments in the company parking lot, they discovered how a single burning cell could ignite the cells around it, triggering a cascading inferno. The company immediately began to investigate this worrying phenomenon of “thermal propagation.”
After discussions with battery consultants – including Voltaiq Advisor, Celina Mikolajczak – and some internal calculations, Tesla came to a conclusion: They needed to design a battery pack that would remain safe even when that pack included a bad cell.
This approach to battery design has defined Tesla’s approach ever since. It has been a core reason why their products are market-leading, and why they are the most highly valued automobile company on earth (by market cap).
Investigating the Cause of High-Profile Recalls
Faced with the challenge of cell-level defects and the dangers of thermal propagation, how are OEMs coping?
Let’s assume a worst case scenario, where a modern OEM gets one defective cell in every million from their supplier. (And Six Sigma, the gold standard of quality control, predicts more than that: 3.4 defects per million.) Given that defect rate, what would we expect to see across the fleets of some EV models in the news today?
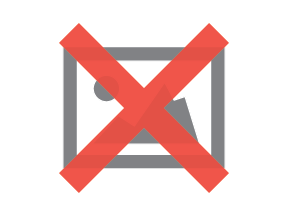
Expected frequency of packs with a defective battery cell
Of these, it is the Hyundai and Chevy models, built with smaller numbers of much larger that are currently facing billion-dollar recalls. Let’s compare these figures to the frequency of fires reported in these recalled models, relative to the number of vehicles sold:
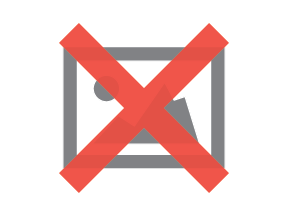
Frequency of reported fires in vehicle fleets
The takeaway here is this: For these two recalled models, the expected frequency of packs containing bad cells is close to the frequency of fires reported across the fleet.
What differentiates the automobiles that have suffered recalls from those that haven’t? Glance at the first table again. Tesla uses ten to twenty times as many cells per pack as Chevy or Hyundai.
Related Posts
The 2023 Battery Report
Battery Industry Trends: Key Insights and Trends from the Volta Foundation
Decoding the Heartbeat: Unlocking Battery Production Efficiency with Data
Subscribe to the Building Better Batteries Newsletter.
Written for battery engineers and leaders in the battery industry. Find resources, trends, and insights from some of the world's top battery experts.