South 8 achieves faster development cycles and higher pilot production yields with Voltaiq.
South 8 used Voltaiq to transform how they derive insight from battery process development and testing, driving faster progress and ensuring consistent, quality products.
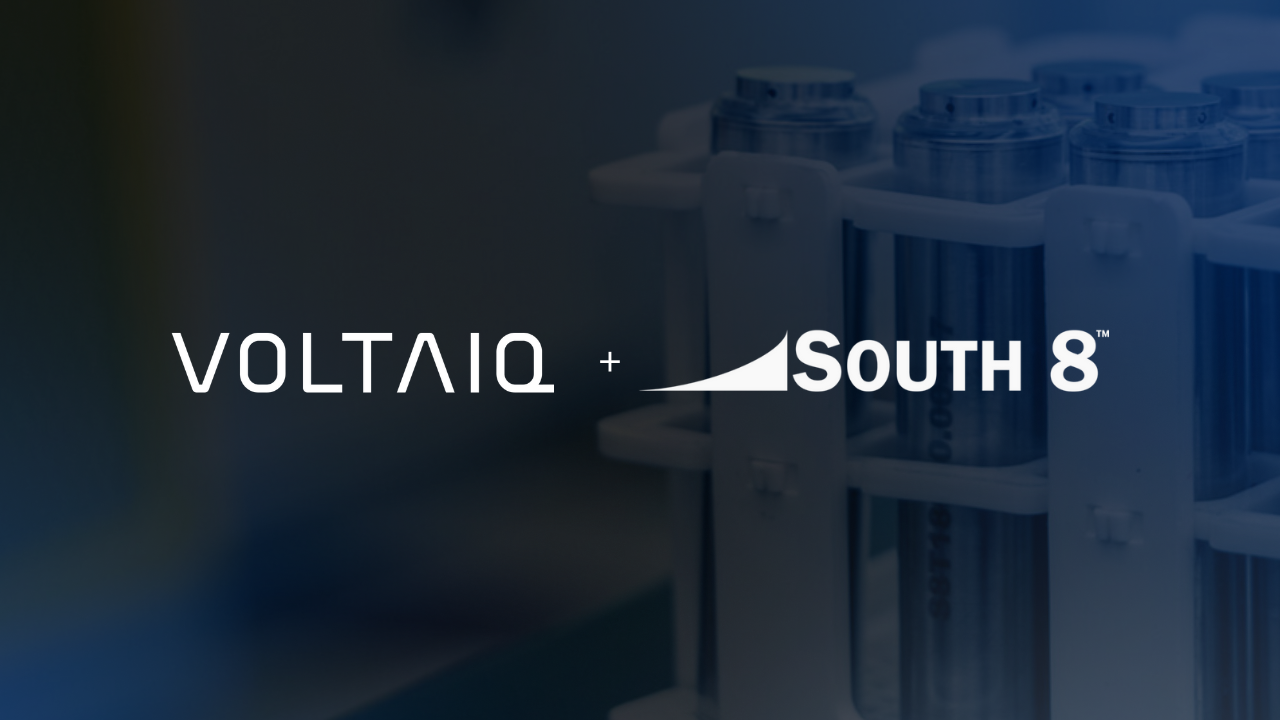
The Problem
As South 8 scaled from R&D to pilot production, their team faced increasing challenges with battery data workflows. Engineers spent valuable time manually collecting data from individual cyclers, cleaning it, and creating reports rather than using insights from the data to move their program forward. Battery cycling data was also siloed from process metadata, obscuring which parts of the process were driving good or bad results. The inefficiency of accessing and processing data from various types of testing equipment became a significant barrier to progress.
“I was really frustrated by the inefficiency of getting the data in front of people's eyes," says Jungwoo Lee, CEO and Co-Founder of South 8 Technologies. “The inefficiency of having to go to every physical cycler to look at data, or going to every physical cycler to export data and then put them on a central computer is the key barrier that I was trying to solve."
The Solution
- Easy access to clean test result data in real time
- Faster, deeper analysis capabilities
- Pinpointing and resolving upstream process and material issues
Easy access to test results in real time.
Before Voltaiq, it was difficult for South 8 engineers to collect, clean, access, and share battery test data. With Voltaiq, data is uploaded in real time and cleaned in a common format, ready to use at any time by anyone on the team. Users can build essential plots of test results in seconds, whereas before it took hours or days.
“My team can make a workspace. They can dump in the kinds of information we're interested in, it automatically updates, and then we can all see it in real time," explains Jungwoo. “And it's not so much about we're stuck in Excel, oh, copy paste that here, readjust that here… we can see it. We can make a choice.”
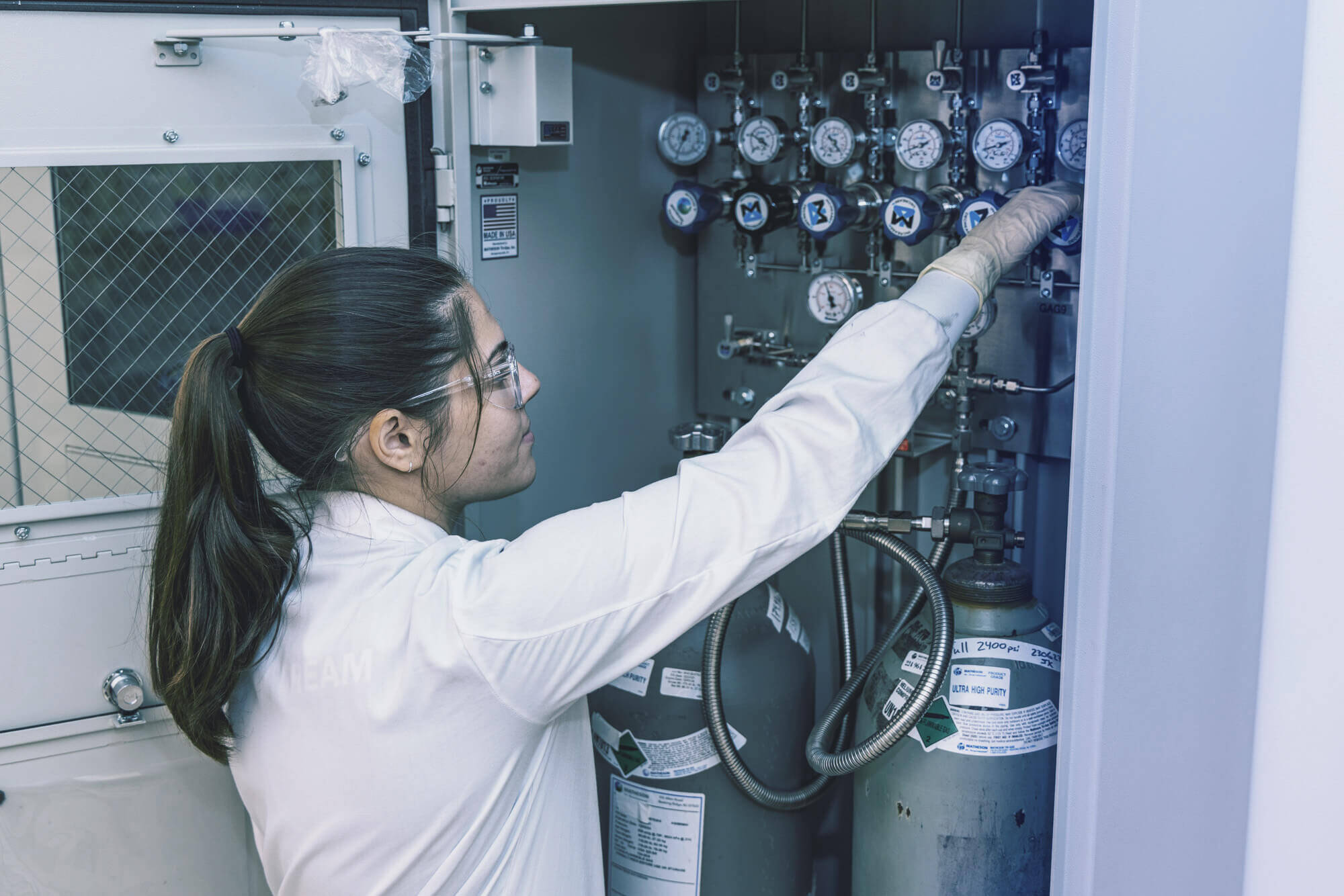
Faster, deeper analysis capabilities.
Hours previously spent manually cleaning data and manually plotting in Excel are now spent making quick, data-led decisions that move their programs forward faster. Engineers have a more intimate relationship with the data, and can derive deeper insights, faster than before.
“When one of my team members started integrating a lot of dQ/dV plots... you could spend probably hours just playing with your own manual filters to try to clean up that data, let alone getting multiple data sets in a beautiful gradient," notes Jungwoo. “You can spend more time focused on what the data is telling you."
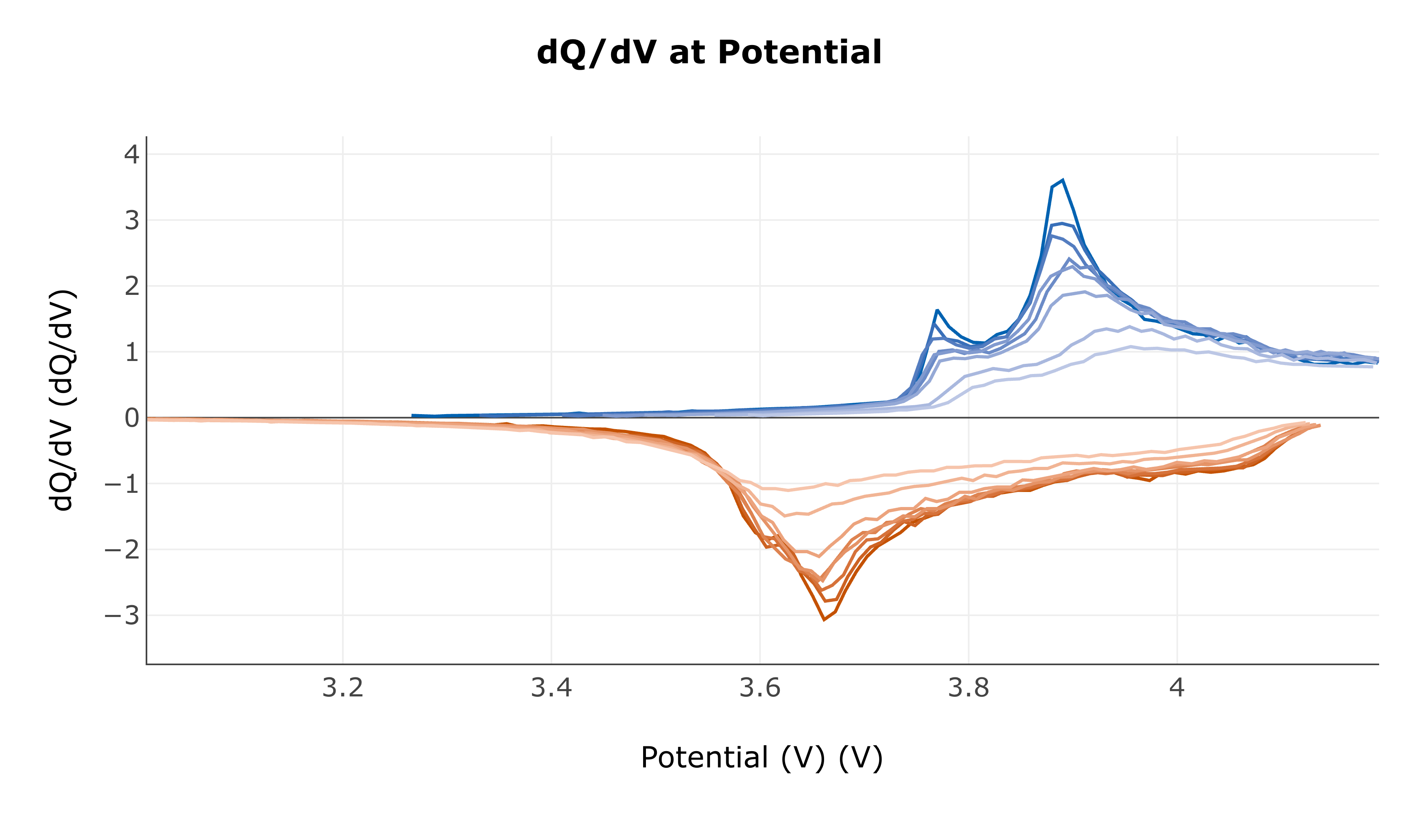
Pinpointing and resolving upstream process and material issues.
As South 8 scaled to pilot production, Voltaiq became essential for correlating battery issues to the upstream processes and materials that caused them. Engineers can catch anomalies in real time, find the root cause, and correct issues in hours compared to days or weeks.
“We've set up a pilot line to demonstrate a lot of these concepts. And through that, what we also learn is a lot of the challenges that people have when they're making a lot of changes on their line and when they're trying to chase down performance metrics. And so, with Voltaiq, we've been able to integrate metadata into our system so that when we do have anomalous electrochemical signals, we're then able to track down key features of that production process."
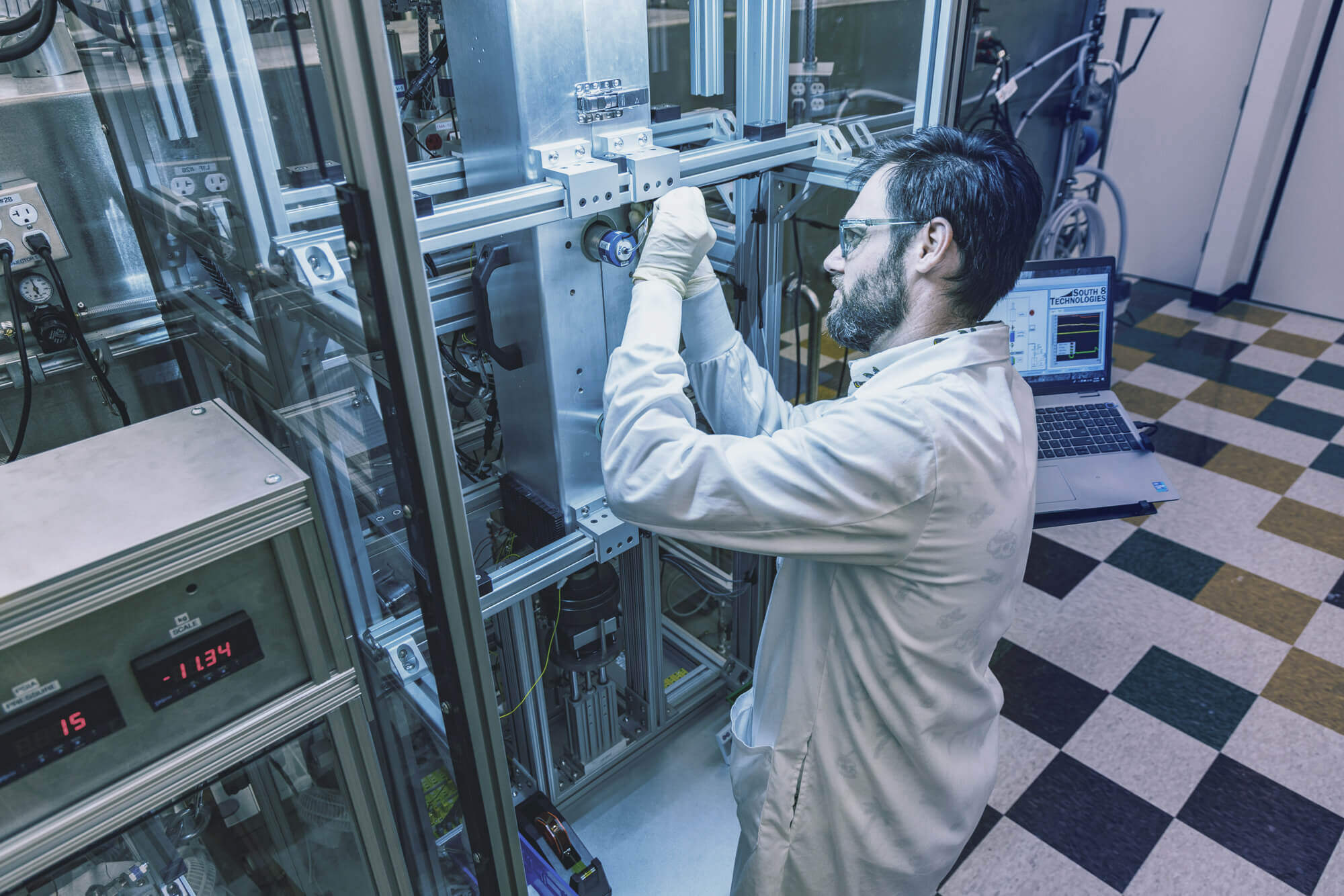
Impact
South 8 has credited Voltaiq with dramatically improving their development speed and production quality. “We had a week where we had a very large deviation in performance and I looked through probably six to seven different steps in the manufacturing line and we're able to dig down exactly where it was because there were a lot of changes happening at the same time," shares Jungwoo.
The platform has democratized data access across the organization, enabling a culture of data-driven decision making. This has been particularly valuable for new team members who can now access and analyze data without specialized training on each piece of testing equipment.
"You have a new cohort of engineers who are used to that mentality of saying the data's at my fingertips, I can check it whenever I want, I don't need to walk over there with my thumb stick, I can share it with my manager, get their feedback immediately, and then get back to work."
The most significant impact has been saving time—South 8's most precious resource. “I think the greatest KPI is those time savings, the time savings to do root cause analysis and FA and then actually containment and then deployment of solutions or faster time in terms of process development."
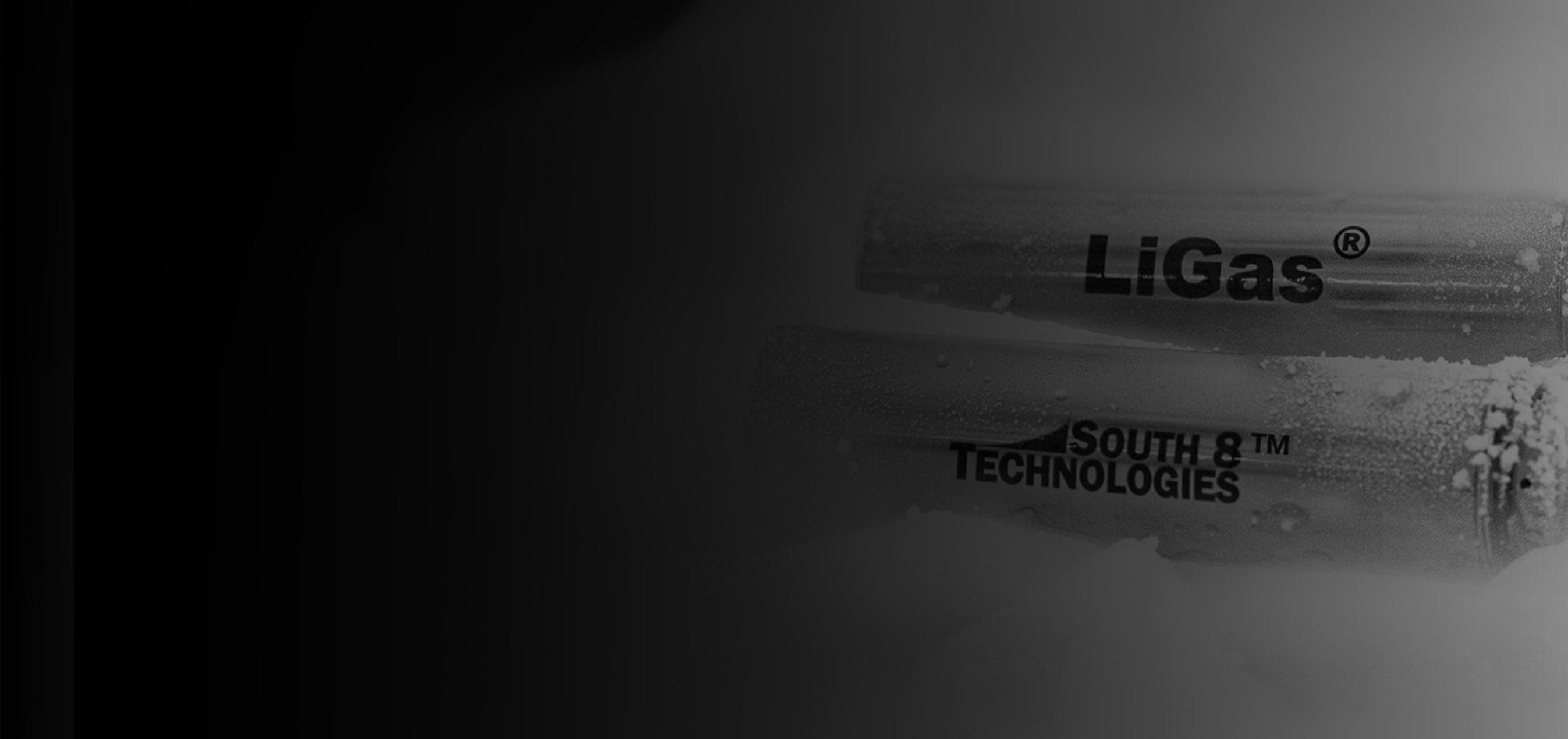
About South 8 Technologies
South 8 Technologies, Inc. develops, manufactures and licenses LiGas®, the liquefied gas electrolyte for advanced lithium-ion batteries that solves lithium-ion's "fire and ice™" problems. South 8's patented LiGas electrolyte reduces fire risk and operates across a wide temperature range, from -60 to 60 °C.
South 8's innovative technology, named to TIME's List of the Best Inventions of 2024, enables clean battery power to benefit more applications, environments, and people. LiGas is also compatible with common battery materials, increases energy, supports fast charging, and is cost effective for battery manufacturers. Headquartered in San Diego, South 8 has introduced its first in a family of LiGas battery cells, Arctic™ LiGas 18650, with new form factors and additional battery chemistries in development.
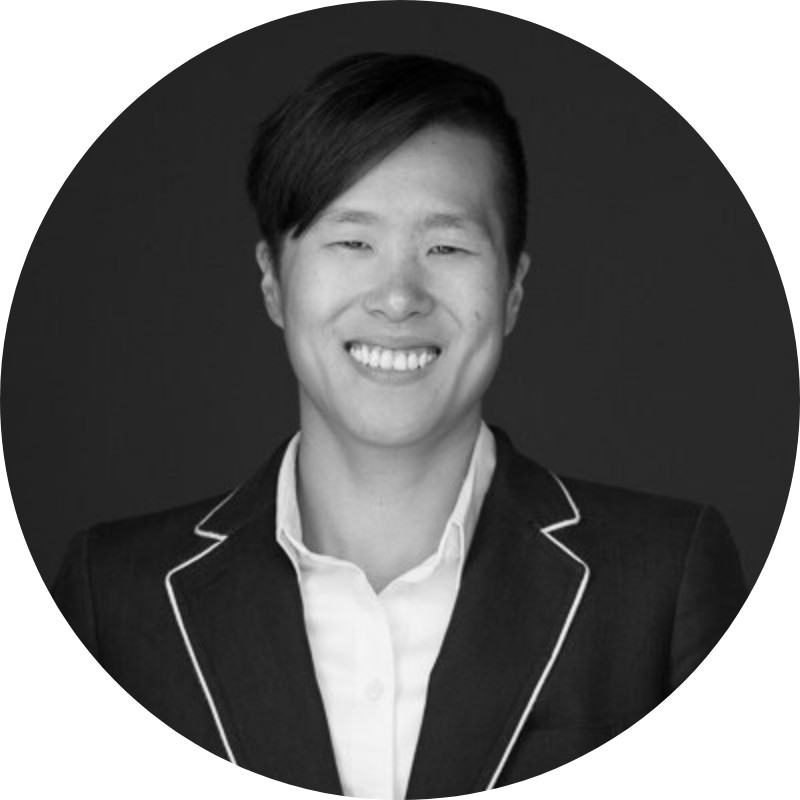
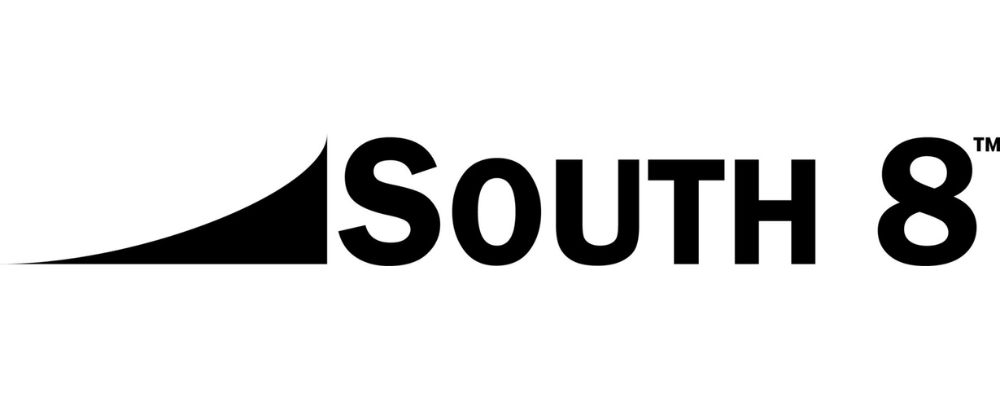
" The most precious resource is time. Those time savings to do root cause analysis and FA and then containment and deployment of solutions, faster time in terms of process development... it all comes down to yield target. Along with a cost target, right? It all goes hands in hand.”
Better business decisions start with a better understanding of your batteries.
Ready to get started?